Spiral Welded Steel Pipes SSAW
Spiral Submerged-Arc Welded Steel Pipes
SSAW Steel Pipe (Spiral Submerged Arc Welded) is manufactured using the spiral welding process, where hot-rolled steel coils or narrow steel strips are continuously shaped into a cylindrical form and welded along a spiral seam. This manufacturing method allows to produce steel pipes of large-diameter, making SSAW pipes ideal for oil and gas, pipeline transportation systems, piling, and structural applications.
The spiral welded structure provides excellent mechanical properties and efficient material usage, ensuring high strength and reliability. These pipes are commonly used in gas transportation, liquid transportation, and large-scale pipeline infrastructure projects.
Advantages of Spiral Welded Steel Pipes:
- High Structural Integrity – The spiral welding process provides strong mechanical performance and load-bearing capacity.
- Large Diameter and Versatility – SSAW pipes can be manufactured in various sizes, making them suitable for the oil and gas sector and natural gas infrastructure. They can also be used as welded structural hollow sections in construction.
- Efficient Production – SSAW pipes are manufactured from hot-rolled steel coils or narrow-strip steel, maximising material efficiency and reducing production costs.
- Enhanced Corrosion Resistance – To ensure long-term durability in harsh environments, spiral welded steel pipes can be supplied with hot-dip galvanising, external protective coatings, or specified elevated temperature properties.
- Strong Seam Welding – Using spiral submerged arc welding (SSAW) technology, the weld seam is highly uniform and secure, minimising risks of air holes or structural weaknesses.
Our Supply Capabilities
- Custom Lengths and Diameters: We can supply spiral welded pipes in various lengths, diameters, and wall thicknesses tailored to your project requirements.
- Premium Material Selection: SSAW pipes are produced from high-quality hot-rolled coils, steel strips, and fine-grain steels to ensure reliable performance and strength.
- Compliance with International Standards: Our SSAW pipes meet industry standards for oil and gas transport, liquid transmission, piling, and construction sector use.
- Coating Options: We offer various protective coatings upon request to extend service life. Surface Treatments: Fusion Bond Epoxy Coating, Coal Tar Epoxy, 3PE, Vanish Coating, Bitumen Coating, Black Oil Coating.
- Optimised Cost and Logistics: We ensure cost-effective delivery with flexible logistics solutions.
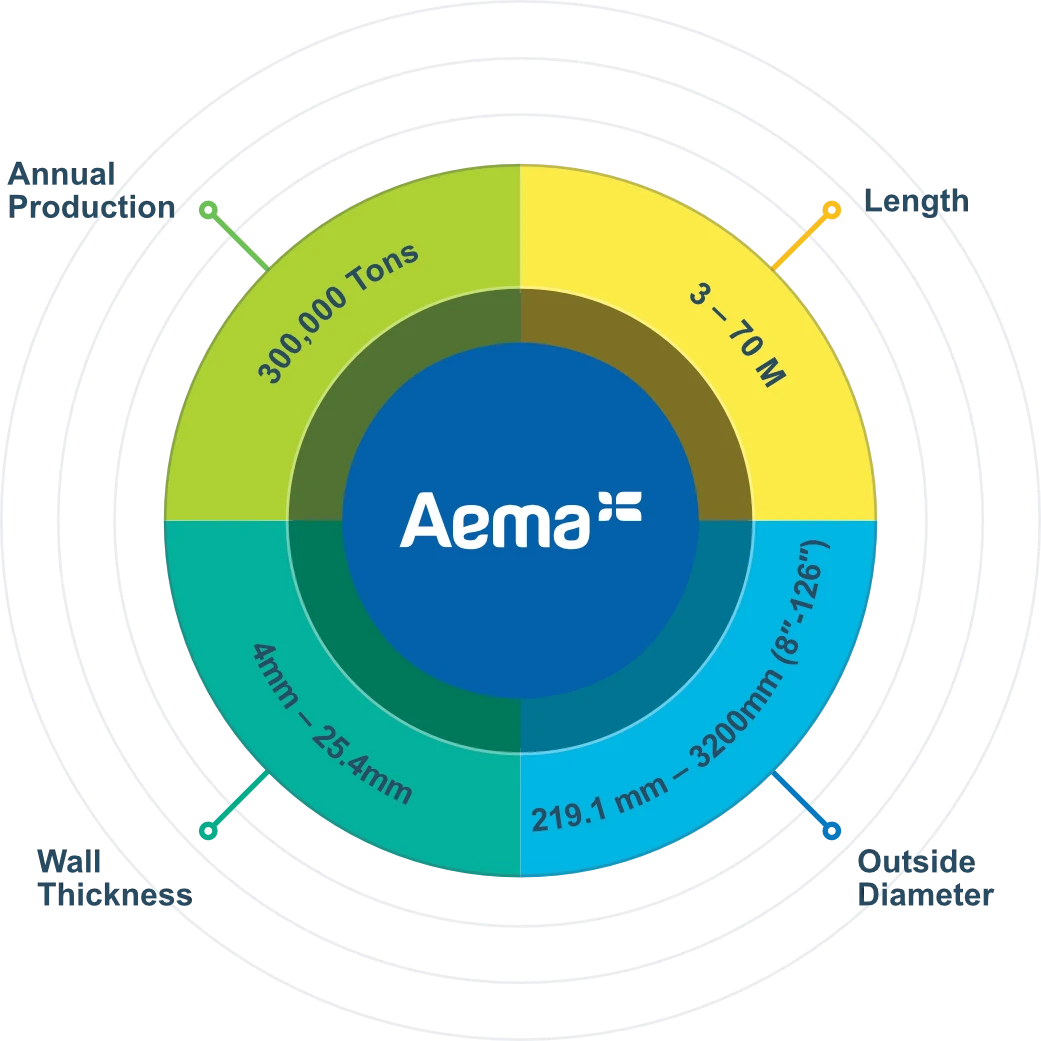
Outer Diameters: 219.1 mm – 3200mm
Wall Thickness: 4mm – 25.4mm
Length: 3 – 70 M
Certificates: EN10217 / EN10219 / API 5L PSL1 / PSL2 / API 5CT
Note: Custom surface treatments are available upon request.
Terms of Supply and Payment Schedule
Considering the manufacturing and delivery times from our exclusive global partners, which might take as long as 30 – 90 days, we offer flexible payment terms including:
- A minimal advance payment for order confirmation.
- Flexibility to pay after the products are delivered to your warehouse or construction site.
- Up to 90 days instalment plans or deferred payments available.
Steel Structures and Custom Steel Fabrication Services
Design of sheet piles, pipe piles and H beams walls
Our tailored selections of type, specification and grade of sheet piles, pipe piles, and H beams (or their combination) ensure optimal profiles, weight, and the number of driving operations. Each solution is engineered and designed to balance cost-effectiveness, durability, quality and logistics.
Factory production of steel structures and welding
Our custom services of manufacturing metal structures and parts of structures and steel welding provide optimised design solutions tailored to specific conditions of the site, loading and unloading operations, transport, storage, and large-module assembly.
Cost optimisation for delivery and assembly of metal structures
We conduct a comprehensive analysis to optimise your expenses, ensuring cost-effective delivery and on-site assembly of metal structures. By evaluating cargo plans, hard-to-reach locations and hidden connections, we optimise the process from procurement to installation on-site.