What we will cover:
-
Sheet piling safety protocols;
-
Equipment and steel sheet piles maintenance;
-
Documentation throughout the project;
Construction sites involve multiple construction activities and are inherently dangerous environments. Safety, maintenance, and documentation are key to a successful sheet piling project. This guide covers guidance on safety practices, maintenance, and documentation to ensure quality control, compliance, and project success. Ensuring safety should always come first in piling operations.
Sheet Piling Safety Protocols on Construction Site
Safety is the top priority when working with heavy machinery, underground utilities, variable soil and often near water. Implementing robust safety protocols is crucial not only to protect people and adjacent structures but also to ensure the success of the project.
Safety Training and Protective Gear
Every worker on the construction site should be trained in the following:
Equipment Operation: Training on operating heavy machinery like hammers and jacking systems for pile driving or handling.
Emergency Procedures: Clear instructions on what to do in case of equipment failure, soil instability or other risks during specific tasks.
Use of Protective Safety Gear: Workers must wear personal protective equipment (PPE), including hard hats, safety glasses, gloves, and hearing protection. Life jackets are required for overwater operations. Workers should consistently wear their PPE while on-site.
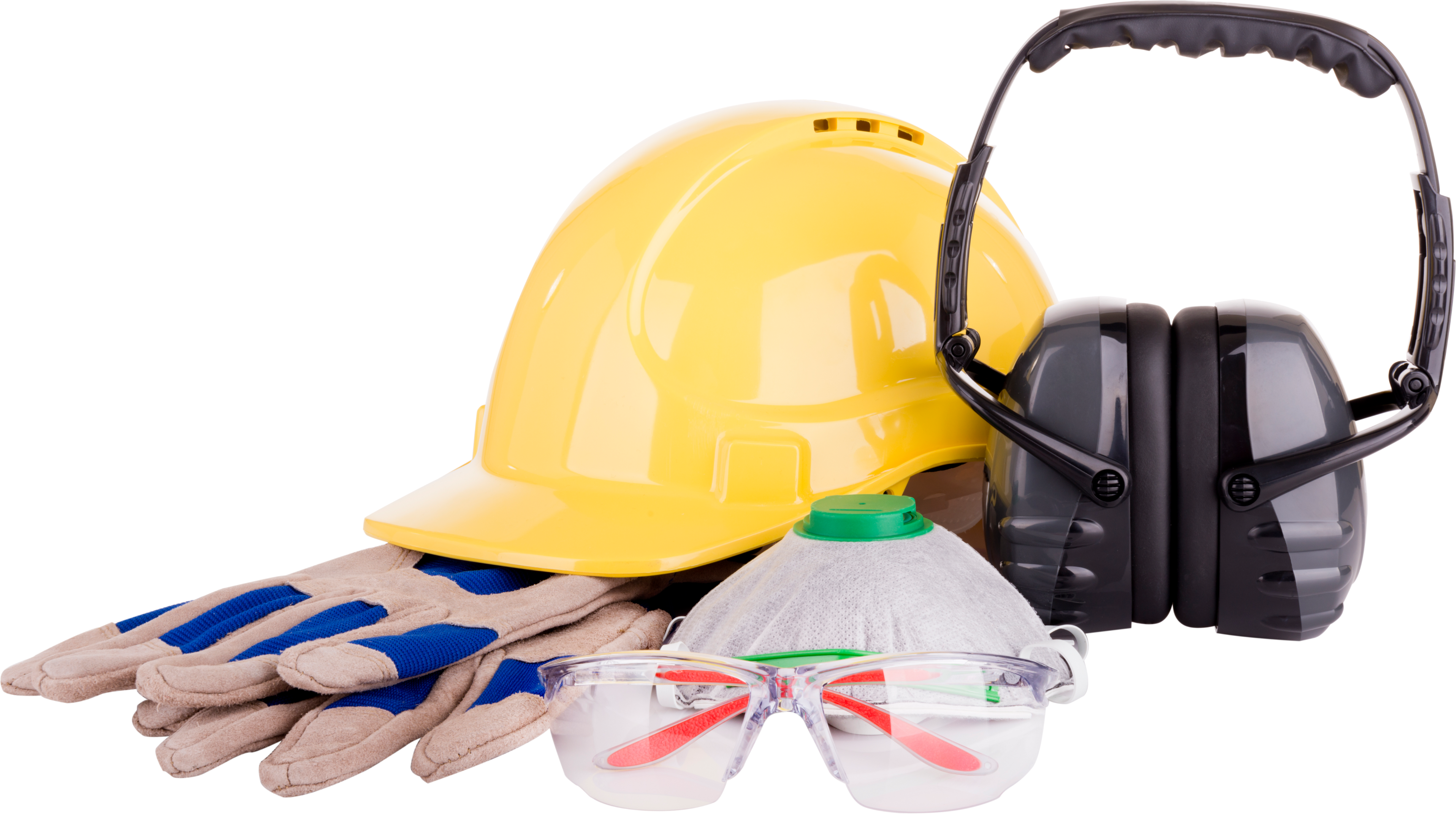
Weather and Site Monitoring: Monitor weather conditions and site-specific hazards and have clear protocols for stopping work if conditions become unsafe.
Clear Communication Protocols: Use hand signals, radios or construction site-wide alarms for quick communication, especially in emergencies. Effective communication is the cornerstone of safety on a construction site.
Signs on Construction Site: Place clear, visible signs throughout the construction site to indicate hazards, restricted areas, PPE requirements, and emergency evacuation routes to prevent injuries and slippage incidents. Proper signage helps to give precautions, reinforce safety protocols, guide workers and visitors, and prevent accidental entry into dangerous, strictly prohibited zones.
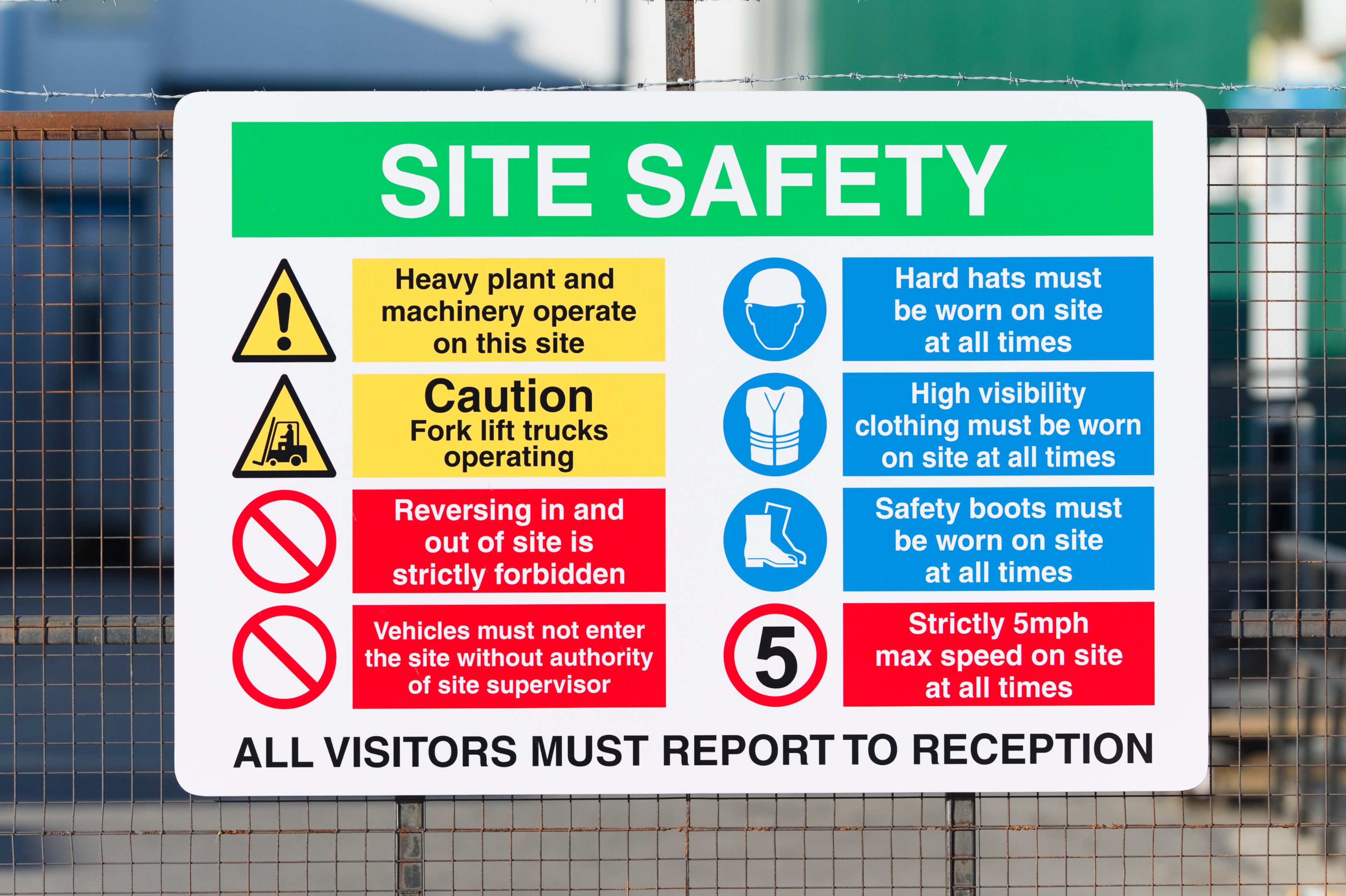
Certification and Compliance for Personnel and Equipment
Certifications are crucial for specific tasks for safety and quality in sheet piling projects. Personnel involved in critical tasks like equipment operation, welding and inspections should have the relevant certifications to prove their expertise and adherence to industry standards. For example, operators of heavy machinery, piling and lifting equipment may need certifications from recognised safety bodies (such as OSHA or ISO certifications) to demonstrate proficiency and compliance with safety protocols. Certified welders must do any welding on sheet piles, connectors or extensions, as improper welding can compromise the structural integrity of the installation. Equipment certifications are equally important to ensure that machines like hydraulic hammers, jacking systems, and welding equipment meet regulatory standards and are safe to use. Regular audits and inspections of certified equipment should be done to maintain compliance, prevent failures and support the overall safety and success of the project.
Regular Routine Inspections
Sheet piles and the surrounding environment should be inspected regularly to detect and address issues early and prevent potential accidents:
Soil Stability Checks: Look for soil erosion, instability, or compaction around sheet piles, which can affect the structure. A thorough assessment of the soil conditions is critical prior to pile installation.
Pile Interlock Integrity: Ensure interlocking mechanisms are secure after dynamic sinking.
Equipment Wear and Tear: Monitor high-use or high-stress areas for equipment damage. Keep spare parts on hand to avoid project delays due to equipment failure.
Emergency Procedures
Emergency protocols must be established and communicated to all personnel. Immediate action should be taken to rectify any identified safety hazards. Develop an emergency response plan and conduct regular drills to get workers prepared for potential hazards:
Emergency Team: Assign an emergency response leader to coordinate responses to incidents.
Evacuation Routes and Assembly Points: Mark evacuation paths and establish safe assembly points for employees for quick and organised evacuations.
First Aid and Medical Response: Have first aid kits on the construction site and train personnel in basic medical response to treat minor injuries, with protocols for calling medical services if required.
Debris Removal: Keep pathways clear to avoid delays during evacuations.
Corrosion Protection and Maintenance
For high moisture or marine environments, maintenance is ongoing to prevent corrosion. This includes applying coatings to sheet piles and checking regularly for rust or wear.
Equipment and Steel Sheet Piles Maintenance
Maintenance is key to equipment and sheet pile longevity and reliability. Regular maintenance routine checks prevent breakdowns, ensure safety and keep the project running.
Equipment Maintenance Schedule
Implement a maintenance schedule that includes the following:
Daily: Check fluid levels, hydraulic lines and safety mechanisms before use.
Weekly: Lubricate joints, check wear points and make minor adjustments as required.
Monthly or Quarterly: Conduct full maintenance on high-use equipment, test all safety and hydraulic systems and check for wear and tear or damage.
Daily, weekly, and monthly safety inspections should be structured and documented.
Inventory Management
Keep spare parts in inventory so critical components are available for repair when needed. Examples include hydraulic hoses, filters, and protective coatings. Having spare parts on hand minimises downtime and keeps the project running. Materials stored on site should be secured to prevent sliding or collapse.
Maintenance Records During the Construction Process
Record every maintenance activity, including dates, findings and actions taken. Digital records can be helpful for accessibility and compliance audits and help with accountability, troubleshooting, and historical records for future maintenance planning.
Equipment Manager
Assigning an equipment manager can be very useful for overseeing equipment selection, leasing, use and repairs. This role will ensure equipment is managed well, prevent delays, and keep project timelines.
Recording Progress and Completion
Good documentation will ensure all project stages are recorded for accountability, quality control and regulatory compliance. Here’s the process:
Intermediate Acceptance
Intermediate acceptance involves reviewing completed work to ensure it meets project specifications before proceeding to the next construction phase. Early checks help identify and fix issues before they become costly or affect later stages.
Inspection Reports: Record soil stability, pile alignment and interlock integrity.
Quality Assurance Checks: Record against project specifications and standards.
Completion Documentation
Final documentation records the whole project for transparency, accountability and quality verification. Key elements include:
Design Changes and Adjustments: Record any changes made during installation for future reference.
Material Testing Results: Record strength, durability, and corrosion resistance test results to confirm that the materials meet specifications.
Safety and Incident Reports: Log on-site incidents, safety drills and routine inspections.
Digital Documentation: Use project management software or digital checklists for real-time reporting and records so all documentation is backed up and easily accessible for audits or client reporting.
Compliance and Environmental Records
Ensure all compliance documentation, such as safety audits and environmental impact assessments, is completed. Environmental assessments are especially important for projects near water to prevent contamination or habitat disruption.
Client and Stakeholder Reporting
Report to clients and stakeholders regularly. Progress reports are important, especially on larger projects where stakeholders may need to know the project status. Provide periodic updates during each construction phase and progress reports as part of transparent communication.
Conclusion: Best Practices for Sheet Piling
Sheet piling project management is all about planning, following safety protocols, maintenance and good documentation. Here’s the summary of best practices:
Choose the Right Installation Method: Based on soil conditions, project location and environmental requirements.
Maintenance First: Maintenance is key to safety and reducing downtime.
Operator and Staff Training: Trained operators and construction teams ensure efficient and safe operation.
Follow Safety Protocols: Hard hats, safety glasses, routine inspections and emergency drills are essential.
Document Each Stage: Record everything for quality assurance, compliance and project tracking.
Environmental Protection: Implement procedures for surrounding habitats, especially for overwater projects.
Regular Safety Audits: Conduct regular audits to ensure continuous compliance with safety standards.
Project Review and Feedback: Conduct the final project review and get feedback from the team to identify lessons learned for future projects.
Following these best practices, sheet piling projects can be managed and achieve safety, efficiency and cost effectiveness, providing durable support for various construction applications. With good planning, the right equipment and comprehensive safety measures, sheet piling can be a strong and stable foundation for years to come. Contact a sheet piling expert to tailor your project to your site and regulatory requirements.
Related Products from Aema Steel
- Hot Rolled U Type Sheet Piles
- Hot Rolled Z Type Sheet Piles
- Cold Formed U Type Sheet Piles
- Cold Formed Z Type Sheet Piles
- Steel Pipe Piles
- Welded H Piles
Contact us today to receive a tailored offer for your upcoming project.